As the demands placed on crash test facilities become ever more complex and diverse.
From zero-emission drives and active safety systems to connected mobility and autonomous driving, the automotive industry is preparing for a major leap in innovation. The demands placed on new crash test facilities and test systems are equally significant. We have to plan for a future that, for some time, we’ve only be able to imagine. This is a huge challenge for everyone who wants to design and implement future-proof automotive test platforms for the years to come.
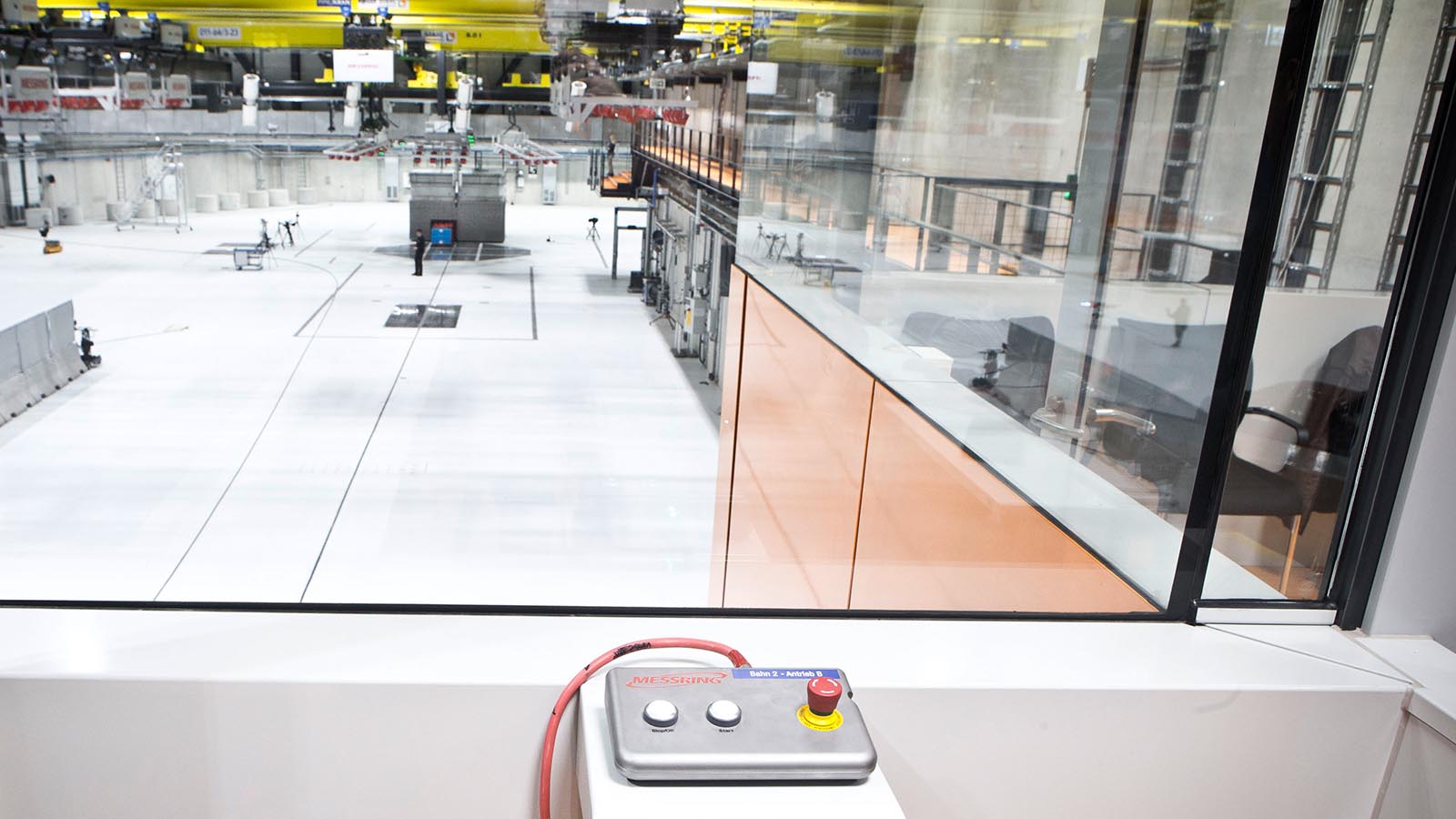
When Arp looks back at the past two or three years at MESSRING, one thing becomes clear: “More and more customers need us to be a developer and problem solver.” MESSRING stopped focusing long ago exclusively on the construction of crash test facilities and their components around the world, and instead also examines the highly specialized issues of general road safety.
Best example is the Mercedes-Benz technology center for vehicle safety (TFS) in Sindelfingen, which was commissioned in late 2016. MESSRING played a key role in planning, developing, and implementing the facility. The TFS center presents safety engineers with brand-new testing options, for instance focusing on car-to-car tests with self-driving and propelled vehicles, assistance system configuration, and vehicle concepts with alternative drives. In the future, it will be possible to synchronize self-driving and propelled vehicles for crash tests in a column-free, roofed-over space measuring 90 by 90 meters. The evasive and braking maneuvers initiated by driver assistance systems in the pre-crash phase can therefore be incorporated into tests using both dummies and, for the first time, vehicles that are moved through the facility. Driver assistance systems can thus be pushed to their limits in a targeted and controlled fashion. Questions that are important to vehicle developers, including how effective assistance systems are and how the vehicle body and passengers move both before and after the actual accident, can now be studied with greater precision. The TFS center will carry out up to 900 general tests and 1,700 sled tests per year. Creating this unique infrastructure required a great deal of development work, including at MESSRING.
Plant Control System
An example of system control: The TFS center has several crash areas, four of which can be independently operated and controlled at the same time if necessary. Around 70 different crash test configurations are possible for cars and trucks. Alone the roofed-over section of the crash hall is larger than an international soccer field. The longest crash track is also well over 200 meters long. No other facility can compete with the dimensions and sheer number of subsystems and peripheries.
Unavoidable consequence: Linear bus systems for distributing switching and trigger signals such as those currently used to control modern crash test facilities have reached their limits in terms of precision, handling, and reliability, so a new solution had to be found for facility control and, in particular, switching and trigger distribution.
MESSRING delivered the facility promptly and, for the first time, developed a digital high-frequency communication infrastructure in the form of M=SYNC, which sends data packs to the most remote locations of the enormous, highly complex facility at the speed of light and without disruption. The linear bus system has been replaced by a virtually infinitely expandable network with trigger boxes, which are connected to each other using several kilometers of fiber-optic cable. Via the global system, all devices receive an identical trigger signal as well as their individual switching rates.
MESSRING also programmed its own communication protocols for no less than 24 difference scenarios for configuring the entire facility. These can be accessed with the press of a button and ensure that individual crash areas can also be isolated and used individually without losing time, which is essential to ensuring efficient facility operation.
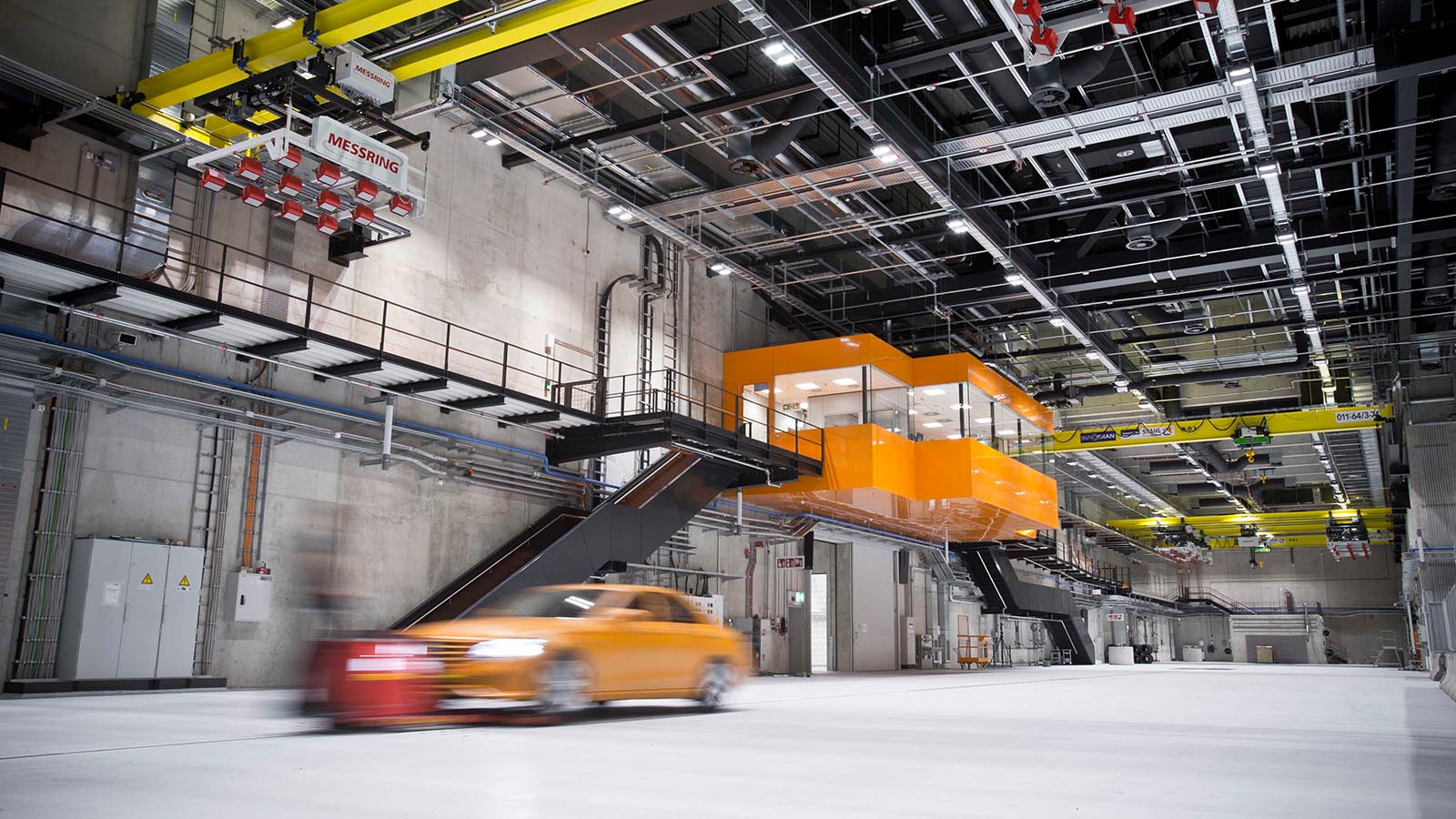
M=SYNC was developed by specialists in a variety of disciplines, with electrical and mechatronics engineers and software developers at MESSRING initially developing no less than five prototypes for the pilot series in order to subject the infrastructure to extensive testing. It took more than 6,700 project hours to turn the initial idea into a finished product. It was the bundled expertise of the interdisciplinary team that ultimately led to success.
Mobile crash block
MESSRING was also able to draw on its strengths when developing the world’s first unconditionally movable crash block, and distinguish itself as a brainstorming partner and idea developer. The task set out by Mercedes-Benz was to develop a self-driving block that, despite its weight of 110 metric tons, enables unrestricted, safe, and relatively uncomplicated navigation within the crash hall. No cable bundles to get in the way or specific routes to follow. Instead: maximum flexibility and relatively simple handling.
MESSRING therefore put together an interdisciplinary development team that, from the ground up, planned the concept of the movable block using existing MESSRING products. The giant block was equipped with overhauled hydraulic travelling gear, a new rechargeable battery system, and sensor technology. The system for anchoring and locking the block on the floor was also revised. Experts ultimately integrated a laser-controlled navigation system for better navigation in the hall.
Around 20 specialists from a variety of areas such as construction, automation, programming, laser technology, mechanics, and electrical engineering worked on the project, occasionally at the same time, creating a self-driving block that can be sent to any location in the hall within just a few minutes. Like the standard model, the four impact sides are preconfigured with different barriers and various test scenarios can be prepared for simply by turning the block.