Uncompromising measurement results at the highest level, easy to implement and modularly applicable.
The precise measurement and recording of forces and loads arising in the event of test vehicles colliding with walls, blocks or barriers is a fundamental component of almost all crash test protocols. For this purpose, a reliable, robust and easy-to-operate system is not only desirable but indispensable in everyday testing. The M=WALL from MESSRING provides comprehensive and at the same time flexible possibilities for data acquisition as well as unsurpassed accuracy of measurement results for vehicle crash tests.
The central components of the innovative load cell wall are the 12.5 cm large cells, which can be variably assembled to form a load cell wall of almost any size. The cells not only record the force distribution on impact in three directions (straight ahead in the direction of travel as well as vertically and transversely), but also calculate torques. The sensors thus include a total of five axes in the representation of the impact energy and thus draw an exact image of the vehicle impact on the load cell wall. The measuring principal of the M=WALL thus provides a much more accurate spatial resolution on the 125 mm cells than comparable products. The position resolution precisely marks the centre of gravity of the forces that arise during the impact. The sensors of the load cell are extremely stable and can provide precise measurement results up to a force of 400 kilonewtons (kN).
Another advantage of the M= WALL is its user-friendliness, since the data acquisition system is integrated into the cells. With the M=BUS system, all cells can be connected or even exchanged in a very short time if a cell needs to be recalibrated. Furthermore, the M=BUS concept allows automatic position detection of the cells in the overall system. The measurement results are convincing with a deviation in linearity over the entire measuring range of less than one percent. When using the MESSRING Crashsoft 3 software, the results are recorded directly and easily and can be exported for precise evaluation. A connection to other common crash test software is also possible.
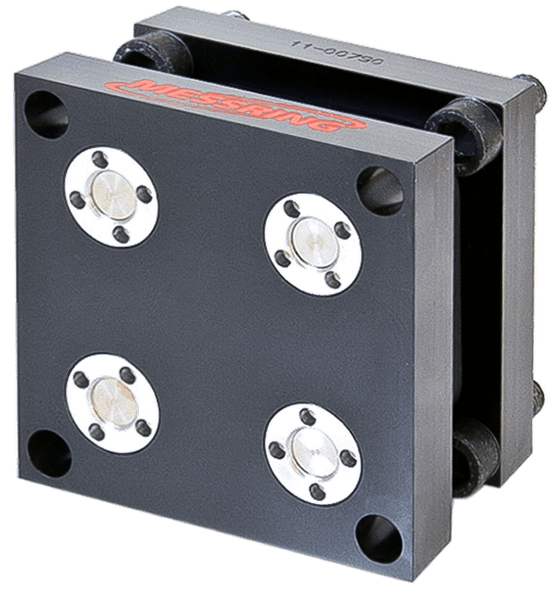
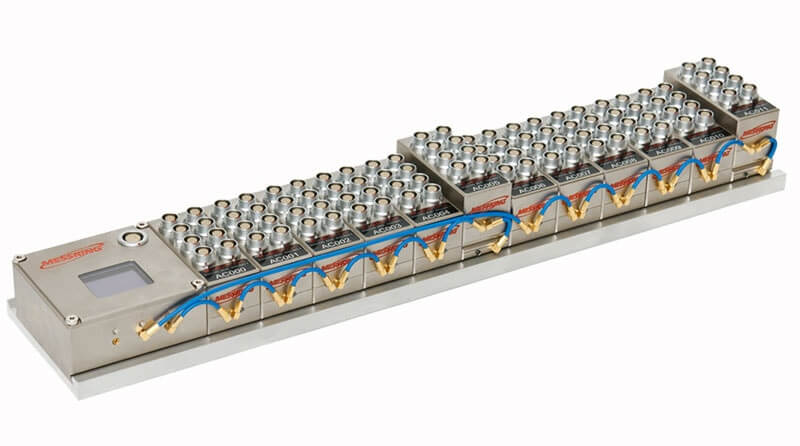
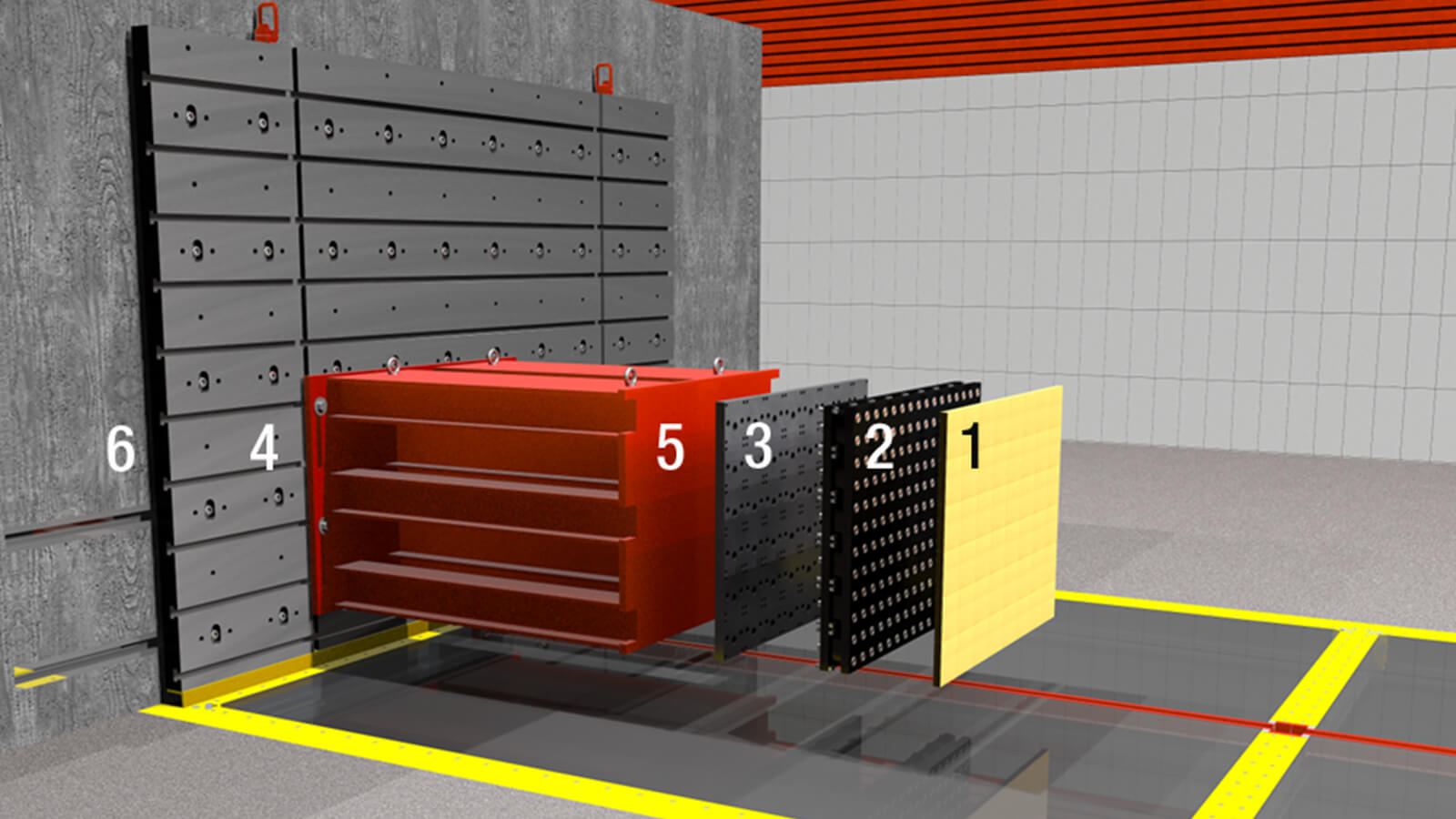
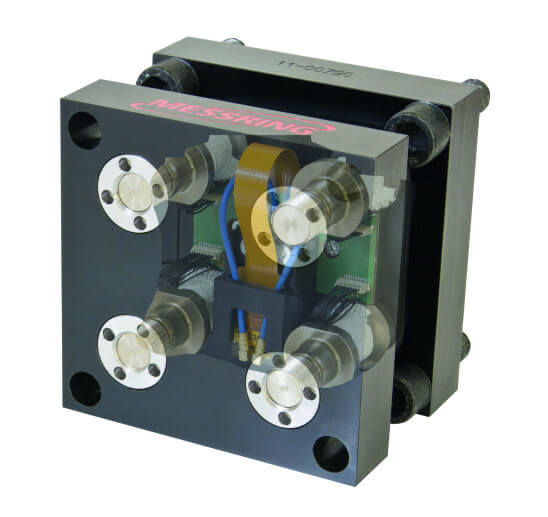
User friendly and variable
The main applications of the load cell wall are the analysis of the structural design of automobile bodies and the testing of the compatibility of the impact behaviour of different vehicles in an accident. Structural analysis is concerned with identifying and eliminating construction-related deficiencies in the structure of an automobile. Vehicle compatibility focuses primarily on the question of how body structures behave when cars of different heights collide frontally or laterally, for example when a small car collides with an SUV. Due to the increasingly strict regulations and requirements for vehicle structures, the issue of compatibility in particular is becoming an important criterion for testers and car body manufacturers of all vehicle brands worldwide.
The measuring cells in the load cell wall can be arranged in nearly any way to provide the desired surface area for standard tests and specific test setups. MESSRING can deliver the walls individually, for example to realize a EURO NCAP offset test as well as the Small Overlap Test. Common sizes of the wall are 2 x 1 meter (16 x 8 cells) or 1 x 1 meter (8 x 8 cells) This flexibility in combination with the uncompromising data acquisition with the M=BUS system saves a lot of time in everyday operation and opens up even more possibilities: For example, the cells can be used to simulate a curbstone crash. This is achieved by arranging and anchoring the 12.5 centimeter high load cells in a line on the ground.
Complex special constructions such as the integration into a test sled like the M=SLED Small Overlap are possible.
The newly developed test sled is designed for use with the MESSRING HydroBrake and is consistently designed to realistically display the small overlap test scenario on the left side of the vehicle. The chassis to be tested runs freely rolling on the ground at up to 64 km/h against a M=WALL load cell which is designed in the contour and curvature of the Small Overlap Barrier and is decelerated in a controlled manner until it breaks. Thanks to the additional load cell, which is based on the shape of a wheel housing and travels on the sleds, the resulting forces and deflection of the components in the wheel housing are efficiently recorded. The ability to record force distributions in five dimensions means that the measuring cells are also perfectly suited for use in angled and rounded constructions and provide reliable measurement results.
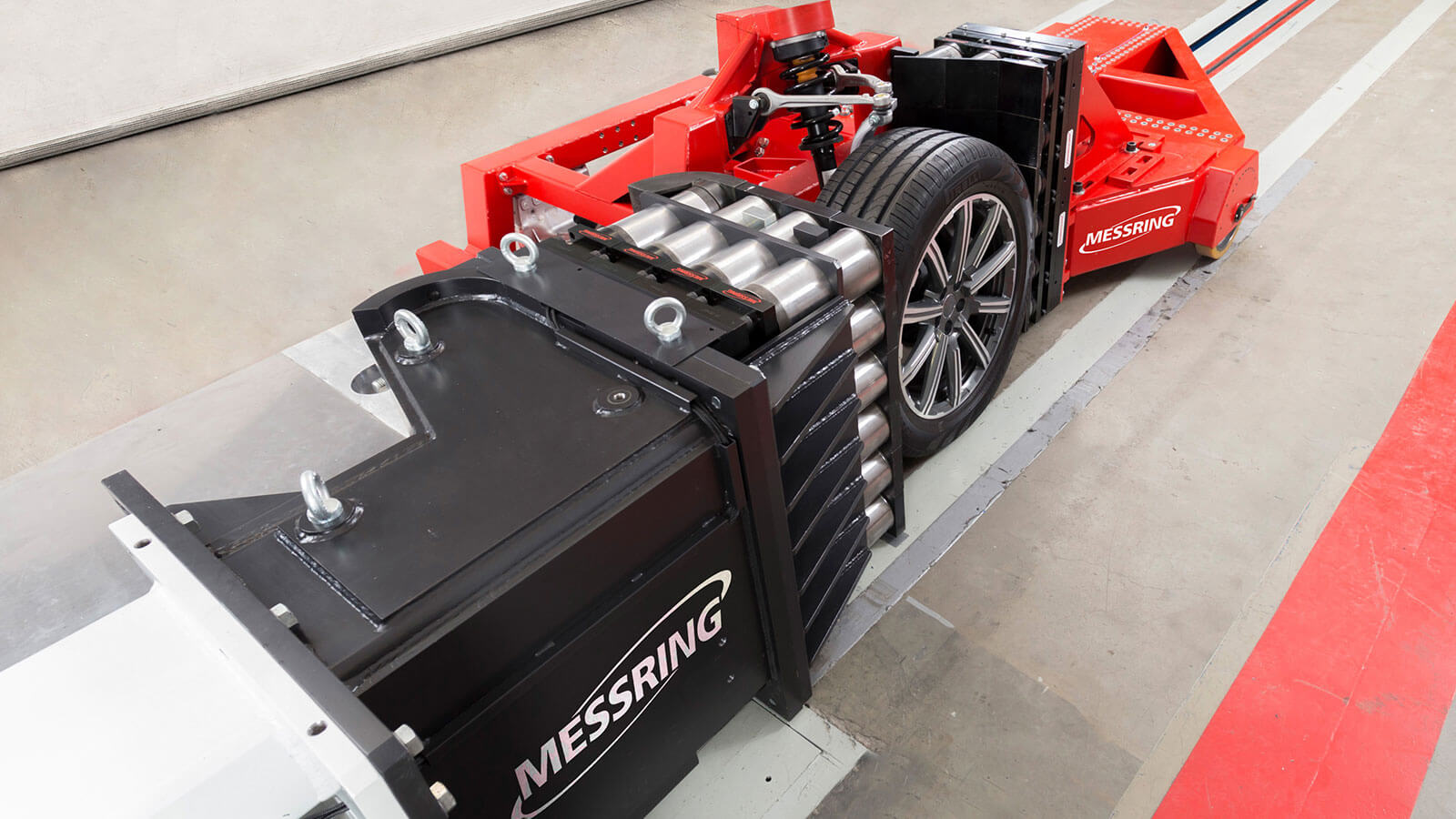
A further scenario is for example the installation of a vertical row of cells in a pole barrier, as prescribed by the EURO NCAP protocol. With the measurement data obtained, the very first prototypes can be tested during the development work and important insights gained. Especially in view of the changes that electric vehicles with their completely changed vehicle structures and masses due to battery packs and frames mean for car manufacturers, a deep understanding of the new behavior of body and structure in early development stages is critical.